压缩空气管道流量计算方法与技术实施指南
- 字号 + -
压缩空气作为工业领域核心动力源,其管道流量计算是保障设备效率、诊断泄漏及优化能源管理的关键环节。本文从气体状态方程、管道参数、流量计选型及实际场景适配出发,系统梳理压缩空气管道流量的计算方法,为机械工程师、设备维护人员及能源管理人员提供实用参考。
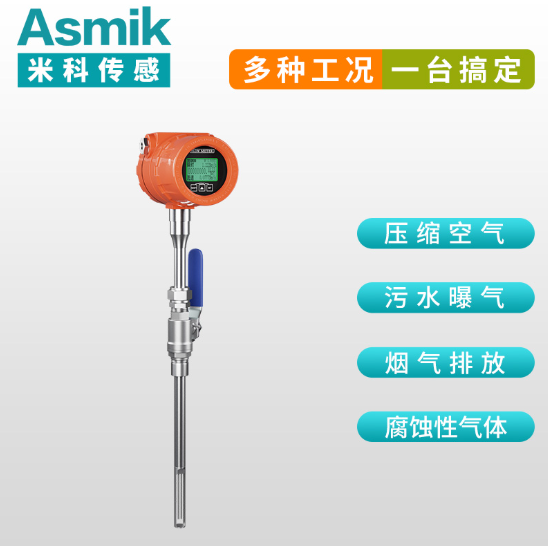
一、压缩空气管道流量计算的核心原理与挑战
压缩空气流量计算需结合气体动力学与热力学原理,其核心挑战包括:
- 状态变化:压缩空气在管道中因压力、温度变化导致密度波动,需通过补偿算法修正。
- 管道阻力:管道长度、直径、粗糙度及弯头、阀门等局部阻力显著影响流量,需通过经验公式或实验数据修正。
- 测量精度:需满足不同场景的精度要求(如工厂能源核算误差≤3%,设备调试误差≤5%)。
主流计算方法可分为理论公式法与流量计实测法两类,前者适用于设计阶段或简单系统,后者适用于复杂或需实时监测的场景。
二、理论公式法:基于气体状态方程的流量计算
理论公式法通过气体状态方程(如理想气体定律)与管道阻力公式,结合已知参数推算流量,适用于设计阶段或初步估算。
1. 基本公式推导
压缩空气流量(Q)可通过以下公式计算:
Q=4πd2⋅v其中,d 为管道内径(m),v 为空气流速(m/s)。
空气流速(v)可通过伯努利方程与达西-魏斯巴赫公式联立求解:
v=ρ(fdL+∑K)2ΔP- ΔP:管道压力损失(Pa)
- ρ:空气密度(kg/m³,需通过温度、压力修正)
- f:管道摩擦系数(可通过莫迪图或科尔布鲁克公式计算)
- L:管道长度(m)
- ∑K:局部阻力系数之和(如弯头、阀门等)
2. 关键参数确定
-
空气密度(ρ):需根据压缩空气的实际压力(P)与温度(T)修正,公式为:
其中,R=287J/(kg\cdotpK),压力P需转换为绝对压力(如表压0.6MPa对应绝对压力0.7MPa)。
- 摩擦系数(f):对于光滑管道,可近似取f=0.02;对于粗糙管道,需通过科尔布鲁克公式迭代计算。
- 局部阻力系数(K):常见元件的K值如下:
- 90°弯头:K=0.75
- 闸阀(全开):K=0.17
- 突然扩大/收缩:K=0.5
3. 适用场景与限制
理论公式法适用于以下场景:
- 管道布局简单(如直管段占比>80%),局部阻力可忽略。
- 压缩空气参数稳定(如压力波动<5%,温度波动<10℃)。
其局限性包括:
- 忽略空气粘性、湍流等因素,误差可能>10%。
- 需手动输入大量参数(如管道长度、粗糙度),实际工程中难以精确获取。
三、流量计实测法:高精度与智能化的流量计算
流量计实测法通过安装专用设备(如孔板流量计、涡街流量计)直接测量流量,适用于复杂系统或需实时监测的场景。
1. 常用流量计类型与原理
-
孔板流量计:通过管道中安装孔板,利用流体流经孔板时产生的压力差计算流量,公式为:
其中,C 为流出系数(需通过实验标定,通常取0.6-0.7)。
-
涡街流量计:通过检测流体流经涡街发生体时产生的涡旋频率计算流量,公式为:
其中,f 为涡旋频率(Hz),St 为斯特劳哈尔数(通常取0.2)。
- 热式质量流量计:通过测量流体流经加热元件时的热量损失计算质量流量,适用于低流速场景(如压缩空气泄漏检测)。
2. 选型与适配
- 管道直径:根据流量范围选择流量计口径(如流量100m³/h需选用DN80流量计),避免超量程导致误差。
- 介质特性:压缩空气含油、水或杂质时,需选用耐腐蚀材质(如316L不锈钢)或带过滤装置的流量计。
- 环境适应性:高温环境(>60℃)需选用带散热片的流量计,低温环境(<-20℃)需选用带加热功能的流量计。
3. 安装与调试
- 安装位置:流量计应安装于管道水平段,上游需保留10倍管径、下游5倍管径的直管段(如DN80管道需上游80cm、下游40cm无阀门或弯头)。
- 调试要点:上电前检查接线极性,避免短路;通过标准源施加已知流量(如50m³/h),验证输出信号线性度(误差<3%)。
四、压缩空气流量计算的实际应用与优化
流量计算需结合具体场景进行参数修正与系统优化,以下为典型应用案例:
1. 泄漏检测与能源管理
- 问题:压缩空气系统泄漏率通常达20%-30%,导致能耗浪费。
- 方法:通过夜间全厂停机时测量管道流量,若流量>0,则存在泄漏;结合超声波检漏仪定位泄漏点(如管道接头、阀门)。
- 优化:修复泄漏点后,重新计算流量并对比能耗数据,验证节能效果。
2. 设备选型与系统设计
- 问题:压缩机选型过大或过小均会导致效率低下。
- 方法:根据设备用气量(如气动工具、喷涂设备)计算总流量,并预留10%-20%余量;通过流量计实测验证设计流量是否合理。
- 优化:采用变频压缩机,根据实时流量调整输出压力,减少空载能耗。
3. 管道布局与阻力优化
- 问题:管道弯头过多或直径过小导致压力损失过大。
- 方法:通过理论公式法计算不同布局下的压力损失,选择阻力最小的方案;通过流量计实测验证优化效果。
- 优化:将90°弯头替换为45°弯头,或将管道直径从DN50扩大至DN80,可降低压力损失30%-50%。
五、总结
压缩空气管道流量计算需结合理论公式法与流量计实测法,根据场景需求选择合适方法,并通过参数修正与系统优化提升准确性。关键要点包括:
- 明确计算目标,优先选用理论公式法(简单系统)或流量计实测法(复杂系统)。
- 适配实际参数,通过温度、压力补偿修正空气密度,通过直管段要求减少局部阻力影响。
- 平衡精度与成本,根据场景需求选择3%-5%精度,避免为不常用功能支付溢价。
通过系统化实施,压缩空气管道流量计算可为工业生产提供准确的数据支撑,助力设备高效运行与能源节约。