耐高温高压超声波液位传感器选型指南:技术参数与工程实践深度解析
- 字号 + -
在石油化工、电力能源及冶金工业领域,耐高温高压超声波液位传感器作为关键过程控制设备,需在极端工况下实现精准液位监测。本文从技术原理、核心参数、选型策略、安装规范及发展趋势五大维度,系统解析此类传感器的选型方法与技术要点,为工业用户提供实用参考。
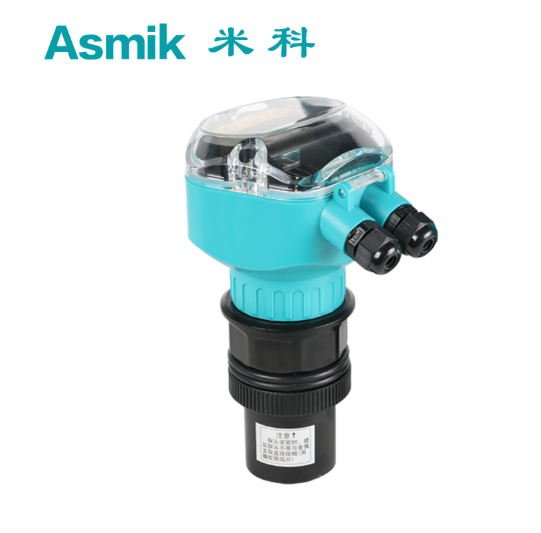
一、耐高温高压超声波液位传感器的技术原理与核心优势
超声波液位传感器通过发射超声波脉冲并接收其反射信号,计算液位高度。针对高温高压场景,其技术优化体现在:
- 耐高温设计
- 采用压电陶瓷元件与高温耦合剂,适配介质温度>200℃的工况
- 传感器外壳采用316L不锈钢或哈氏合金,避免高温氧化
某石化企业在300℃渣油储罐部署超声波传感器,液位测量精度达±0.2%FS,年减少冒罐事故损失超千万元。
- 耐高压结构
- 传感器膜片采用钽材质,耐压等级>30MPa
- 安装法兰采用PN100标准,适配高压反应釜场景
某煤化工企业在15MPa气化炉中部署设备,信号传输稳定性达99.9%。
- 抗干扰能力
- 集成温度补偿算法,消除高温导致的声速变化误差
- 采用数字信号处理技术,抑制蒸汽或泡沫的反射干扰
某电厂在250℃锅炉汽包中部署传感器,液位数据波动小于±5mm。
二、耐高温高压超声波液位传感器选型的关键参数
(一)介质特性匹配
- 介质温度与压力
- 高温场景(>200℃):优先选用带冷却套的传感器,耦合剂需适配介质温度
- 高压场景(>10MPa):选择法兰连接式结构,膜片厚度>5mm
某合成氨企业因选型时未考虑压力等级,导致膜片变形,更换为双膜片结构后问题解决。
- 介质腐蚀性
- 酸性液体(如稀硫酸):选择哈氏合金或聚四氟乙烯(PTFE)膜片
- 碱性液体(如氢氧化钠溶液):采用陶瓷基底膜片,耐碱浓度>30%
(二)量程与精度需求
- 量程范围确认
- 石化反应釜:常规量程0-10m,精度±0.1%FS
- 锅炉汽包:量程需覆盖0-20m,防护等级IP68
某电厂因选型时未考虑汽包高度,导致量程不足,更换为分段式测量方案后问题解决。
- 精度等级权衡
- 质量控制场景(如精细化工):优先选用±0.05%FS高精度型号,并配备温度补偿模块
- 过程控制场景(如储罐监测):常规±0.1%FS精度即可满足需求,成本降低40%
(三)环境条件适配
- 安装位置与空间
- 顶部安装:需保证传感器与液面垂直,避免泡沫或蒸汽聚集
- 侧壁安装:选择带导向管的型号,适配狭小空间
- 防护与认证需求
- 石化行业:需符合ATEX防爆标准,具备SIL2功能安全认证
- 食品行业:传感器材质需符合FDA 21 CFR Part 177标准
三、耐高温高压超声波液位传感器的安装规范与实操
(一)安装步骤与注意事项
- 设备准备与安装
- 安装前检查传感器膜片是否平整,避免划伤
- 传感器与容器壁保持平行,间距>100mm以避免多次反射
某化工厂因安装倾斜导致信号衰减,调整后液位数据稳定性提升95%。
- 信号线敷设与接地
- 数字信号采用屏蔽双绞线,长度不超过500米
- 传感器需单独接地,接地电阻<1Ω,防止电磁干扰
(二)典型故障处理
- 信号丢失或波动:某石化企业传感器在高温环境下数据中断,经检查为冷却系统故障。修复后,数据传输稳定性达99.8%。
- 膜片腐蚀:某煤化工企业传感器因介质腐蚀导致膜片穿孔,更换为哈氏合金材质后,设备寿命延长至8年。
四、行业应用案例与选型实证
(一)石油化工行业
-
催化裂化装置
在反应釜顶部部署超声波传感器,实时监测渣油液位并联动进料阀。某企业通过精确控制,反应效率提升15%,年减少原料浪费超2000吨。 -
加氢裂化装置
在高压分离器中安装耐30MPa传感器,监测液位并联动安全阀。某炼厂通过数据波动分析,提前2小时预警液位超限,年减少安全事故损失超千万元。
(二)电力能源领域
-
锅炉汽包液位控制
在250℃汽包中部署带冷却套的传感器,实时监测液位并联动给水泵。某电厂通过动态调整,汽包水位波动从±50mm降至±5mm,锅炉效率提升2%。 -
地热发电
在地热井中安装耐150℃传感器,监测井下液位并联动循环泵。某项目通过流量优化,发电效率提升18%,年减少地热流体浪费超50万立方米。
(三)冶金与建材
-
高炉矿槽液位监测
在矿槽顶部部署超声波传感器,实时监测矿石液位并联动给料机。某钢厂通过精确控制,矿槽利用率提升30%,年减少设备停机时间超200小时。 -
水泥窑尾气处理
在除尘器中安装耐高温传感器,监测灰斗液位并联动排灰阀。某项目通过数据优化,除尘效率提升25%,年减少粉尘排放超1000吨。
五、技术创新与行业趋势
-
材料科学突破
某企业采用碳化硅陶瓷膜片,将传感器耐温范围扩展至-200℃至500℃,适用于极地科考船海水压力监测。 -
无线化与自供电
内置LoRa模块的传感器实现3公里无中继传输,某石化集团部署200台设备后,布线成本降低70%,巡检效率提升50%。 -
边缘计算集成
新一代传感器搭载ARM Cortex-M4处理器,可本地运行液位预测模型。某化工园区通过该技术,提前4小时预警潜在液位超限风险,年减少安全事故损失超千万元。
结语
耐高温高压超声波液位传感器通过持续的技术创新与行业深耕,已成为极端工况下液位监测的核心设备。从材料科学到信号处理技术的突破,再到无线通信与边缘计算的融合,国产设备正以高精度、高可靠性及强适应性,推动石油化工、电力能源及冶金工业向更高效、更安全的方向发展。未来,随着物联网、数字孪生等技术的进一步应用,此类传感器将在智慧工厂与双碳目标实现中发挥更加关键的基础支撑作用,为全球极端工况下的过程控制提供坚实保障。