搅拌罐超声波液位测量技术解析:原理、挑战与行业适配方案
- 字号 + -
在化工生产、食品加工及制药工程领域,搅拌罐作为核心反应容器,其液位精准测量对工艺控制、设备安全及产品质量至关重要。超声波液位计凭借非接触式测量、安装便捷等优势,成为搅拌罐液位监测的常用方案。然而,搅拌过程中产生的泡沫、漩涡及介质波动,对超声波测量精度构成显著挑战。本文系统阐述搅拌罐超声波液位测量的技术原理、实施方法及行业适配方案,为工程技术人员提供实用指导。
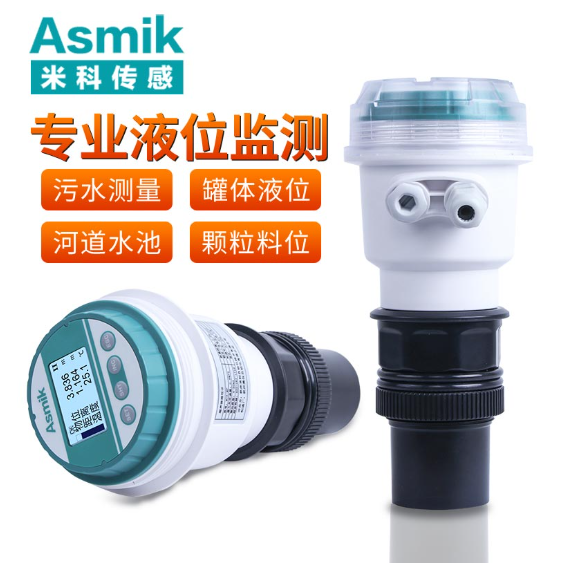
一、超声波液位测量的核心原理与技术挑战
(一)超声波测距基本原理
- 工作原理
- 超声波液位计通过发射脉冲超声波,测量发射与回波的时间差计算液位,公式 H=21⋅v⋅Δt(v 为声速,Δt 为时间差);
- 优势:非接触式测量,适用于腐蚀性或高温液体,量程覆盖0.1m至50m。
- 搅拌罐中的特殊挑战
- 泡沫干扰:搅拌产生的泡沫导致超声波散射,信号衰减严重;
- 漩涡影响:液体旋转运动使声波反射路径偏移,测量值波动;
- 介质波动:液面不稳定导致回波信号识别困难。
二、搅拌罐超声波液位测量的关键技术
(一)泡沫抑制技术
- 发射角度调整
- 选用小角度超声波探头(如8°发散角),减少泡沫对声波的散射;
- 案例:某化工企业通过调整发射角度,将泡沫环境下的测量误差从±10cm降至±3cm。
- 信号滤波算法
- 配置自适应滤波器,识别并剔除泡沫产生的异常回波信号;
- 技术方案:采用小波变换算法,有效分离有效回波与噪声信号。
(二)漩涡补偿技术
- 多探头阵列
- 安装多个超声波探头(如3探头阵列),通过三角测量法抵消漩涡影响;
- 案例:某食品加工厂通过多探头阵列,将漩涡环境下的液位波动范围从±15cm降至±5cm。
- 动态校准模型
- 建立漩涡强度与液位偏差的数学模型,实时修正测量值;
- 技术方案:通过搅拌电机电流信号反推漩涡强度,联动调整液位计算参数。
(三)介质波动抑制
- 平均采样算法
- 连续采集多个测量值(如10次/秒),取中位数或平均值作为最终结果;
- 案例:某制药企业通过平均采样算法,将介质波动导致的测量误差从±8cm降至±2cm。
- 回波追踪技术
- 识别并跟踪真实液面回波,忽略虚假信号(如罐壁反射);
- 技术方案:采用峰值能量检测算法,优先选择能量最高的回波信号。
三、搅拌罐超声波液位测量的实施流程
(一)设备选型与安装
- 探头类型选择
- 小容量搅拌罐(<5m³):选用高频超声波探头(40kHz),分辨率高;
- 大容量搅拌罐(>5m³):选用低频超声波探头(20kHz),穿透性强。
- 安装位置优化
- 垂直安装:探头轴线垂直液面,避免倾斜导致的测量偏差;
- 远离搅拌器:安装位置距搅拌桨中心>30cm,减少漩涡干扰;
- 案例:某涂料厂因探头安装过近,测量值波动范围达±20cm,调整后降至±5cm。
(二)系统校准与调试
- 空罐校准
- 搅拌罐空载时,记录探头至罐底的初始距离 H0;
- 步骤:输入 H0 至控制器,作为液位计算的基准值。
- 满罐校准
- 注入已知体积液体,记录探头至液面的距离 H1;
- 步骤:输入 H1 至控制器,验证量程与线性度。
- 动态调试
- 启动搅拌电机,观察液位测量值波动范围;
- 调整参数:优化滤波算法强度、平均采样次数等参数,确保波动<±5cm。
(三)日常维护与故障处理
- 探头清洁
- 周期:每24小时用干燥压缩空气吹扫探头表面,避免介质附着;
- 案例:某乳品厂因探头结垢,测量误差从±3cm升至±15cm,清洁后恢复。
- 信号检查
- 每日:用示波器观察回波信号,确认主峰清晰、无异常噪声;
- 每周:校验空罐与满罐校准值,误差需控制在±1cm以内。
四、行业应用场景与实施案例
(一)化工反应釜液位控制
- 需求特点
- 监测反应釜内液位,防止溢流或干转;
- 液体含催化剂颗粒,表面覆盖泡沫。
- 实施方案
- 选用高频超声波液位计(40kHz),配套泡沫抑制算法;
- 探头安装于釜顶,距搅拌桨中心50cm;
- 效果:液位控制精度从±10cm提升至±3cm,反应釜溢流事故从年均5次降至0次。
(二)食品发酵罐液位监测
- 需求特点
- 监测发酵液液位,控制补料与出料;
- 液体含蛋白质泡沫,表面波动剧烈。
- 实施方案
- 选用低频超声波液位计(20kHz),配套多探头阵列;
- 探头安装于罐顶,配置自清洁功能(每2小时吹扫一次);
- 效果:发酵罐液位波动范围从±15cm降至±5cm,产品合格率提升15%。
(三)制药结晶罐液位控制
- 需求特点
- 监测结晶过程液位,防止晶体沉积干扰;
- 液体透明度低,需穿透晶体悬浮层。
- 实施方案
- 选用穿透式超声波液位计(30kHz),配套动态校准模型;
- 探头安装于罐侧,距罐底10cm;
- 效果:结晶罐液位测量误差从±8cm降至±2cm,晶体沉积导致的设备故障率降低70%。
五、维护与故障处理
(一)典型故障与解决方案
故障现象 | 可能原因 | 解决方案 |
---|---|---|
液位值突变 | 泡沫或漩涡导致信号反射异常 | 增加信号滤波强度,配置泡沫抑制算法 |
测量值持续偏高 | 探头表面污垢或罐壁附着介质 | 启用自清洁功能,定期人工清理 |
无回波信号 | 探头安装位置不当或声速设置错误 | 调整探头角度,重新校准声速参数 |
(二)日常维护要点
- 探头保养
- 每月检查探头表面是否损伤,更换老化密封圈;
- 每季度用酒精擦拭探头透镜,避免介质结晶。
- 系统检查
- 每日确认控制器时间同步,避免数据错位;
- 每周校验空罐与满罐校准值,确保基准准确。
六、总结与行业建议
搅拌罐超声波液位测量需构建"抗干扰设计-精准校准-智能算法"三维体系:
- 抗干扰设计:通过探头选型、安装位置优化及信号处理算法,抑制泡沫、漩涡等干扰;
- 精准校准:严格执行空罐与满罐校准,定期验证测量基准;
- 智能算法:集成自适应滤波、动态校准等技术,提升复杂工况下的测量稳定性。
随着智能传感技术发展,超声波液位计正从单一参数测量向工艺优化终端演进。建议行业加强以下技术研发:
- 基于AI的液位-搅拌强度关联分析模型;
- 结合数字孪生的三维搅拌罐液位场可视化平台;
- 适应极端工况(如高温、高粘度)的新型超声波探头材料。