压力变送器测量液位技术解析:原理、方法与全流程管理
- 字号 + -
在化工生产、水处理与食品饮料加工领域,压力变送器作为将液位高度转换为标准信号的核心设备,其精准测量对工艺控制、安全监控与成本核算至关重要。本文系统阐述压力变送器测量液位的实施原理、操作方法及行业适配方案,为相关从业者提供技术参考。
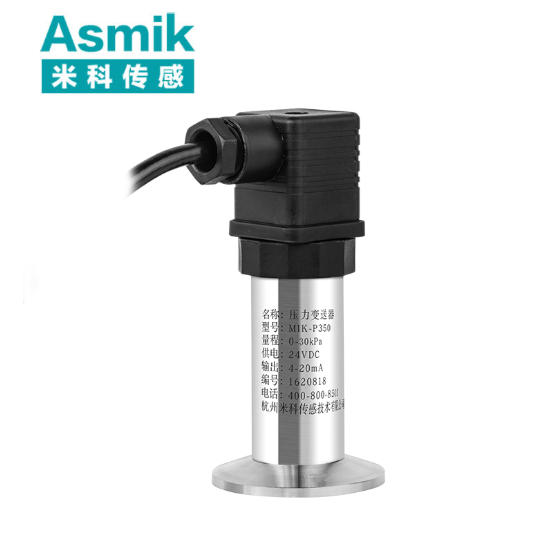
一、压力变送器测量液位的核心原理与技术分类
(一)静压原理
- 基础公式
- 液位高度(H)与压力(P)的关系:P=ρ⋅g⋅H,其中 ρ 为液体密度,g 为重力加速度;
- 优势:原理简单,适用于敞口容器液位测量。
- 设备选型
- 绝压变送器:测量液位静压与大气压之和,适用于非密闭容器;
- 表压变送器:测量液位静压与大气压之差,适用于密闭容器。
(二)差压测量法
- 工作原理
- 通过测量液位底部压力(P高)与顶部压力(P低)的差值计算液位,公式 H=ρ⋅gΔP;
- 优势:可消除液体密度变化的影响,适用于密闭容器或沸腾液体。
- 设备配置
- 差压变送器:需配套正压室与负压室导压管;
- 平衡阀:用于零点校准与导压管排气。
二、压力变送器测量液位的设备与系统组成
(一)核心设备
- 压力变送器
- 类型:工业在线型(防爆、耐腐蚀)或卫生型(316L不锈钢);
- 参数:精度±0.1%FS,量程比≥10:1。
- 导压管与配件
- 材质:316L不锈钢(适用于腐蚀性液体)或PVC(适用于水处理);
- 配件:三阀组(用于差压变送器)、平衡阀、排气阀。
- 数据记录仪
- 功能:存储历史液位数据,支持4-20mA、RS485或以太网通信;
- 参数:存储容量≥1GB,采样间隔可调(1秒-24小时)。
(二)辅助材料
- 校准溶液
- 水(密度1g/cm³)或已知密度的校准液体(如酒精密度0.8g/cm³);
- 校准周期:每6个月手动校准1次,或每3个月自动校准1次。
- 清洁工具
- 软毛刷(用于清除导压管内污垢)、高压气枪(用于吹扫堵塞管道)。
三、压力变送器测量液位的实施流程
(一)设备安装与校准
- 变送器安装
- 位置:敞口容器需安装于容器底部;密闭容器需安装正压室于底部,负压室于顶部;
- 固定:工业场景需配置法兰或卡箍,卫生场景需采用卫生级卡箍。
- 导压管敷设
- 走向:需保持1:100的坡度,避免气泡积聚;
- 长度:差压变送器正负压室导压管长度需一致(误差<5cm)。
- 系统校准
- 步骤:
- 关闭平衡阀,打开正压室排气阀;
- 注入校准液体至零点,稳定10分钟后校准零点;
- 注入校准液体至满量程,校准量程;
- 校准误差需控制在±0.2%FS以内。
- 步骤:
(二)数据采集与监控
- 参数设置
- 采样间隔:根据需求设置(如化工生产设为1分钟,水处理设为5分钟);
- 报警阈值:设置液位上下限(如容器高度的80%-120%),超限时触发声光报警或联动控制。
- 远程监控
- 配置:变送器通过以太网或4G模块接入云平台;
- 功能:实时查看液位曲线、下载历史数据、设置报警参数。
(三)日常维护
- 变送器保养
- 清洗:每24小时用软布擦拭传感器膜片,含杂质液体需用高压气枪吹扫导压管;
- 再生:每7天用校准液体浸泡传感器5分钟,恢复测量精度。
- 系统检查
- 每日:检查导压管是否堵塞或泄漏;
- 每周:校验数据记录仪时间同步,避免数据错位。
四、行业应用场景与实施案例
(一)化工反应釜液位监控
- 需求特点
- 监测反应液液位,防止冒罐或干烧;
- 需防爆认证,适应高温高压环境。
- 实施方案
- 选用差压变送器,配套耐腐蚀导压管与三阀组;
- 数据记录仪设置采样间隔10秒,报警阈值根据反应工艺设定;
- 联动控制进料泵与出料阀,液位超限时自动调节流量。
案例:某化工厂通过实时液位监控,将反应釜液位控制精度从±5cm提升至±1cm,冒罐事故发生率从每月2次降至0次。
(二)市政水厂清水池液位测量
- 需求特点
- 监测清水池液位,优化水泵调度;
- 需长期储存历史数据(>1年),适应户外环境。
- 实施方案
- 选用绝压变送器,配套PVC导压管与防爆型数据记录仪;
- 云平台设置采样间隔1小时,报警阈值池体高度的70%-130%;
- 通过液位趋势分析,将水泵启停频率从每小时5次降至2次,能耗降低30%。
案例:某水厂通过历史液位数据分析,识别出某时段液位异常下降,最终定位并修复一处DN500管道泄漏点,年减少水资源浪费30万吨。
(三)食品饮料行业CIP系统液位控制
- 需求特点
- 监测CIP清洗罐液位,控制清洗成本;
- 需符合食品级卫生标准,易于清洗消毒。
- 实施方案
- 选用卫生型压力变送器,配套CIP专用导压管与数据记录仪;
- 云平台设置采样间隔10秒,报警阈值根据清洗工艺设定;
- 通过液位数据分析,将CIP用水量从40m³/次降至25m³/次,年减少水费支出40万元。
案例:某乳制品企业通过液位储存与分析,优化CIP清洗流程,将设备停机时间从3小时/次缩短至1小时/次,生产效率提升30%。
五、维护与故障处理
(一)日常维护
- 设备保养
- 压力变送器:每6个月用软布擦拭传感器膜片,检查导压管是否堵塞;
- 数据记录仪:每季度清理散热口灰尘,检查存储空间使用率(<80%)。
- 系统检查
- 每日:确认数据记录仪时间同步,避免数据错位;
- 每周:校验云平台与本地存储数据一致性,误差需控制在±0.1%FS以内。
(二)典型故障与解决方案
故障现象 | 可能原因 | 解决方案 |
---|---|---|
液位值偏低 | 导压管堵塞或传感器膜片污染 | 用高压气枪吹扫导压管,更换传感器膜片 |
信号波动剧烈 | 液体流速过高(>1m/s)或气泡干扰 | 安装整流器降低流速,配置消泡装置 |
校准失败 | 传感器老化或电路故障 | 更换新传感器,检查屏蔽电缆接地 |
无输出信号 | 电源故障或通信线路中断 | 检查保险丝与接线端子,更换损坏电缆 |
六、总结与行业建议
压力变送器测量液位需构建"精准测量-实时监控-智能预警"三维体系:
- 测量层面:根据场景需求选择绝压型或差压型变送器,确保导压管敷设规范;
- 监控层面:配置高分辨率数据记录仪与远程云平台,实现本地+远程双备份;
- 预警层面:集成AI算法,实现液位趋势预测与异常预警。
随着工业互联网发展,压力变送器正从单一液位测量向能源管理终端演进。建议行业加强以下技术研发:
- 基于物联网的自动校准与故障诊断系统;
- 结合机器学习的液位预测与优化模型;
- 与数字孪生技术融合的三维容器液位场可视化系统。