污水pH如何检测
- 字号 + -
在污水处理、工业废水排放及环境监测领域,pH值是衡量水质酸碱性的核心指标,直接影响生化处理效率、设备腐蚀风险及排放合规性。PH/ORP控制器通过电位法原理实现pH值的实时监测与控制,成为污水检测系统的核心设备。本文从工作原理、设备选型、安装规范、校准维护及数据处理五大维度,系统解析PH/ORP控制器在污水pH检测中的应用方案,为工程技术人员提供可落地的技术指南。
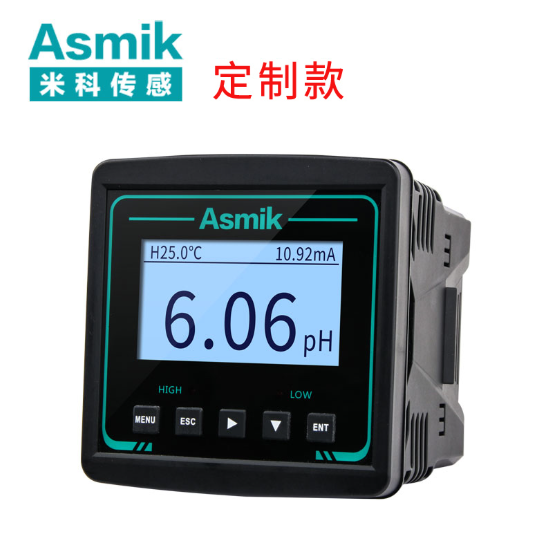
一、PH/ORP控制器的工作原理与核心组件
1.1 电位法测量原理
PH/ORP控制器基于电位法原理,通过pH电极与参比电极构成原电池,测量溶液中氢离子活度对应的电位差:
E=E0−nFRTlnaH+
其中,E 为测量电位,E0 为标准电位,R 为气体常数,T 为绝对温度,n 为电子转移数,F 为法拉第常数,aH+ 为氢离子活度。
1.2 核心组件
组件 | 功能 | 技术要求 | 典型参数 |
---|---|---|---|
pH电极 | 感知氢离子活度 | 玻璃膜耐腐蚀,响应时间<30s | 量程0-14pH,精度±0.02pH |
参比电极 | 提供稳定电位参考 | 电解液为KCl凝胶,寿命>2年 | 内阻<100kΩ |
温度传感器 | 补偿温度对pH的影响 | Pt1000,精度±0.1℃ | 防护等级IP68 |
控制单元 | 信号处理与输出控制 | 支持4-20mA/RS485输出 | 数据存储容量≥1年 |
二、污水pH检测的特殊挑战与技术适配
2.1 污水特性与检测难点
污水pH检测需应对以下复杂工况:
工况类型 | 特征参数 | 典型场景 | 检测难点 |
---|---|---|---|
高腐蚀性 | 含强酸(pH<2)或强碱(pH>12) | 化工废水、电镀废水 | 电极膜材料耐腐蚀性 |
高悬浮物 | 悬浮物浓度>500mg/L | 市政污水、食品加工废水 | 电极污染与信号干扰 |
温度波动 | 温度范围-10℃~80℃ | 生物反应池、热力消毒废水 | 温度补偿精度 |
脂肪与油脂 | 油脂浓度>100mg/L | 餐饮废水、油脂加工废水 | 电极表面润湿性下降 |
2.2 PH/ORP控制器技术适配
- 电极材料选择:
- 强酸环境(pH<2):选用钽材电极或聚四氟乙烯(PTFE)膜电极;
- 强碱环境(pH>12):采用哈氏合金(C-276)电极或陶瓷膜电极。
- 抗污染设计:
- 电极表面加装防污罩(如PTFE滤网),减少悬浮物附着;
- 采用脉冲式清洗装置,定期用低压水流冲洗电极表面。
- 温度补偿策略:
- 内置Pt1000温度传感器,补偿算法符合Nernst方程,温度系数修正范围-10℃~80℃。
三、设备选型与安装规范
3.1 选型关键参数
- 测量范围:根据污水pH波动范围选择量程(如0-14pH或2-12pH),避免量程过宽导致精度下降;
- 精度等级:排放监测场景需满足HJ 969-2018《pH水质自动分析仪技术要求》中2级标准(误差≤±0.1pH);
- 防护等级:户外或潮湿环境选用IP68设备,室内场景可选用IP65;
- 输出信号:根据控制系统需求选择4-20mA(模拟量)、脉冲(计数)或RS485(数字量)接口。
3.2 安装位置与步骤
- 电极安装:
- 垂直插入污水流道中部,深度为电极长度的2/3,避免表面气泡干扰;
- 远离进出水口、搅拌器及化学药剂投加点,与容器壁保持≥10cm距离。
- 参比电极安装:
- 参比系统与pH电极同步安装,确保电解液与污水充分接触;
- 参比电极法兰与管道间加装聚四氟乙烯垫片,厚度≥2mm。
- 电气安装:
- 信号线采用双绞线(绞距≤20mm),屏蔽层单端接地(接控制器端),接地电阻≤4Ω;
- 电源线与信号线分槽布线,间距≥300mm,避免电磁干扰。
四、校准方法与标准规范
4.1 校准步骤(以两点校准法为例)
- 准备标准缓冲液:选用pH 4.01、7.00、10.01的标准溶液,温度与污水温度一致(误差≤2℃);
- 零点校准:
- 清洗电极后浸入pH 7.00缓冲液,调整控制器输出至7.00pH;
- 记录零点误差 E0=pHmeas−7.00。
- 斜率校准:
- 浸入pH 4.01或10.01缓冲液,调整增益使输出至对应值;
- 计算斜率误差 Serror=pHstdpHmeas−pHstd×100%。
- 温度补偿验证:
- 改变缓冲液温度(如25℃→50℃),验证控制器温度补偿功能是否正常。
4.2 行业标准与周期
- 检定规程:依据HJ 969-2018,首次使用及每3个月需送检至法定计量机构;
- 校准周期:高频使用场景(如市政污水处理厂)每2周校准一次,实验室设备每1个月校准一次;
- 文档要求:校准记录需包含环境温度、标准液参数、调整前后数据及验收结论,存档备查。
五、维护策略与故障处理
5.1 日常维护
- 巡检周期:每班次检查电极膜是否破损、电缆连接是否松动;
- 清洗计划:
- 高悬浮物污水:每周用软毛刷清洗电极,高油脂污水每2天用酒精擦拭;
- 参比电极每3个月补充或更换电解液(3mol/L KCl)。
- 存储条件:长期不用时,电极需浸泡在保护液(3mol/L KCl),控制器需置于干燥环境(相对湿度<60%)。
5.2 常见故障与解决方案
故障现象 | 可能原因 | 处理措施 |
---|---|---|
pH值漂移 | 参比电极电解液干涸 | 补充或更换电解液(3mol/L KCl) |
信号波动 | 电源噪声或电磁干扰 | 增加滤波电容,优化屏蔽接地 |
响应迟钝 | 电极膜污染或老化 | 清洗电极,老化严重时更换 |
报警误触发 | 阈值设置过严 | 调整报警延时(如30s)与死区范围(如±0.05pH) |
5.3 报废与更换标准
- 电极老化:膜片出现裂纹、变色或阻抗>200MΩ时需更换;
- 控制器故障:测量误差持续>0.2pH且无法调整时更换;
- 防护失效:防护等级下降至IP65以下或检定超期时报废。
六、结论与行业应用建议
PH/ORP控制器在污水pH检测中需构建“原理适配-精准安装-智能校准-规范维护”全流程体系:
- 选型阶段:依据污水特性(如酸碱度、悬浮物浓度)选择电极材料与防护等级,优先验证样机在模拟工况下的性能;
- 安装阶段:确保电极与参比电极的机械对齐,优化电气屏蔽与接地设计,抑制电磁与温度干扰;
- 校准阶段:采用两点校准法结合温度补偿验证,符合HJ 969-2018检定规程;
- 运维阶段:制定巡检、清洗、校准计划,结合智能诊断工具(如pH趋势分析系统)提前预警故障;
- 技术升级:关注无线通信(如LoRa)与AI算法融合的发展,通过远程监控与预测性维护降低全生命周期成本。
通过系统化管理,企业可将污水pH检测误差控制在±0.1pH以内,为污水处理工艺优化、排放合规性验证及环境风险预警提供可靠数据支撑。