如何实现纯水槽PH及电导率值的在线监控
- 字号 + -
在半导体制造、生物医药及超纯水制备领域,纯水槽的PH值与电导率是衡量水质纯净度的核心指标。PH值反映水中酸碱平衡,电导率则直接关联离子浓度,二者需控制在极窄范围内(如PH 5.0-7.0,电导率<0.1μS/cm)。本文从系统架构设计、传感器选型、数据采集处理、通信传输及维护规范五大维度,系统解析纯水槽多参数水质分析仪在线监控的实现路径,为工程技术人员提供可落地的技术方案。
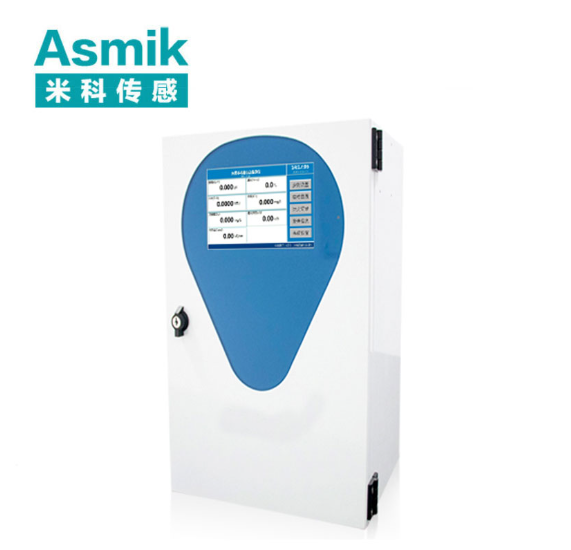
一、系统架构设计:模块化与集成化结合
1.1 核心组件
纯水槽在线监控系统由传感器层、数据采集层、传输网络层及应用层四级架构组成,各层级功能如下:
层级 | 组件 | 功能 | 技术要求 |
---|---|---|---|
传感器层 | PH电极、电导率传感器 | 实时采集水质参数 | 耐腐蚀、高精度、低维护 |
数据采集层 | 多参数分析仪 | 信号调理、A/D转换 | 支持4-20mA/RS485输出 |
传输网络层 | 工业交换机、无线模块 | 数据传输与协议转换 | 符合Modbus TCP/IP标准 |
应用层 | SCADA软件、云平台 | 数据存储、分析、报警 | 支持历史趋势查询与报表生成 |
1.2 系统拓扑
- 小型系统(纯水槽数量<10):采用星型拓扑,传感器直接接入多参数分析仪,数据通过RS485总线传输至本地监控站;
- 大型系统(纯水槽数量≥10):采用环形拓扑,传感器通过无线LoRa模块组网,数据经边缘计算网关聚合后上传至云平台。
二、传感器选型与安装规范
2.1 PH电极选型
- 膜材料:
- 常规纯水:选用普通玻璃膜电极(响应时间<30s,精度±0.02pH);
- 高纯水(电阻率>10MΩ·cm):采用低阻抗玻璃膜电极(阻抗<50MΩ),减少测量噪声。
- 参比系统:
- 长寿命场景:选用凝胶型参比电极(电解液为3mol/L KCl,寿命>2年);
- 高温环境(如CIP清洗):采用双参比电极结构,避免温度冲击导致的液接界堵塞。
2.2 电导率传感器选型
- 量程适配:
- 超纯水(电导率<1μS/cm):选用四极电极(量程0.01-20μS/cm,精度±1%);
- 常规纯水(电导率1-100μS/cm):采用二极电极(量程1-1000μS/cm,精度±0.5%)。
- 温度补偿:内置Pt1000温度传感器,补偿算法需符合ASTM D1125标准,温度系数修正范围-10℃至80℃。
2.3 安装位置与注意事项
- PH电极:
- 垂直插入纯水槽中部,深度为电极长度的2/3,避免表面气泡干扰;
- 远离进出水口、搅拌器及化学药剂投加点,与容器壁保持≥10cm距离。
- 电导率传感器:
- 安装于纯水槽回流管路,确保水流速度0.5-1.5m/s,避免沉积物覆盖电极;
- 传感器法兰与管路同轴度误差≤0.5mm,螺栓紧固力矩控制在20N·m~25N·m。
三、数据采集与处理技术
3.1 信号调理与A/D转换
- PH信号:
- 通过高输入阻抗运算放大器(阻抗>10¹²Ω)调理,避免电极极化误差;
- A/D转换分辨率≥16位,采样频率1Hz,确保捕捉快速pH波动(如CO₂溶解导致的pH变化)。
- 电导率信号:
- 采用交流激励法(频率1kHz),消除电极极化效应;
- 信号经带通滤波器(截止频率500Hz)处理,抑制工频干扰。
3.2 数据校准与异常检测
- 校准周期:
- PH电极:每2周用标准缓冲液(pH 4.01、7.00、10.01)三点校准;
- 电导率传感器:每月用标准溶液(如0.01μS/cm、1μS/cm、10μS/cm)校准。
- 异常检测:
- PH值突变(如ΔpH>0.2/min)时触发报警,并联动纯水制备系统调整加药量;
- 电导率持续上升(如>0.05μS/cm/h)时,启动反渗透膜清洗程序。
四、通信传输与数据展示
4.1 传输协议与网络配置
- 有线传输:
- RS485总线:最大传输距离1200m,支持32个节点,采用CRC-16校验确保数据完整性;
- 以太网:符合IEEE 802.3标准,数据包丢失率<0.1%。
- 无线传输:
- LoRa模块:工作频段470-510MHz,空旷环境传输距离>3km,数据速率0.3-50kbps;
- 4G路由器:作为备用链路,APN专网接入,保障关键数据传输可靠性。
4.2 数据展示与报警
- 本地监控站:
- 采用SCADA软件(如WinCC、iFix),实时显示PH、电导率趋势曲线,支持历史数据查询与报表导出;
- 报警阈值可配置(如PH<5.5或>7.5,电导率>0.1μS/cm),报警方式包括声光提示、短信通知。
- 云平台:
- 部署于AWS、Azure等公有云,支持多纯水槽数据集中管理;
- 提供API接口,可与MES、ERP系统集成,实现水质数据与生产流程的联动控制。
五、维护规范与故障处理
5.1 日常维护
- 巡检周期:每班次检查传感器膜片是否破损、电缆连接是否松动;
- 清洗计划:
- PH电极:每周用软毛刷清洗玻璃膜片,高纯水场景每2天用保护液(3mol/L KCl)浸泡;
- 电导率传感器:每月用0.1mol/L HCl溶液循环清洗,去除电极表面金属沉积物。
- 存储条件:长期不用时,PH电极需浸泡在保护液,电导率传感器需密封干燥保存。
5.2 常见故障与解决方案
故障现象 | 可能原因 | 处理措施 |
---|---|---|
PH值漂移 | 参比电极电解液干涸 | 补充或更换电解液(3mol/L KCl) |
电导率读数异常 | 电极极化或污染 | 改用交流激励法,增加清洗频率 |
数据中断 | 通信链路故障 | 检查RS485终端电阻(120Ω),重启无线模块 |
报警误触发 | 阈值设置过严 | 调整报警延时(如30s)与死区范围(如±0.05pH) |
5.3 报废与更换标准
- PH电极老化:膜片出现裂纹、变色或阻抗>200MΩ时需更换;
- 电导率传感器失效:电极极间电阻>10kΩ或温度补偿误差>5%时更换;
- 精度超标:校准后误差持续>0.1pH或>2%FS且无法调整时报废。
六、结论与行业应用建议
纯水槽PH及电导率在线监控系统的实施需遵循“精准选型-规范安装-智能处理-可靠传输-定期维护”的全流程管理原则:
- 选型阶段:依据纯水槽工况(如温度、流速、离子浓度)选择传感器类型,优先验证样机在模拟环境中的性能;
- 安装阶段:确保传感器位置具有代表性且免受机械损伤,参比系统与电极膜片需完全浸入介质;
- 数据处理阶段:采用高分辨率A/D转换与智能校准算法,结合异常检测逻辑提前干预水质波动;
- 传输阶段:根据系统规模选择有线或无线传输方案,确保数据实时性与完整性;
- 维护阶段:制定清洗、校准、巡检计划,结合云平台远程监控功能降低现场维护成本。
通过系统化管理,企业可将纯水槽PH控制精度提升至±0.05pH,电导率测量误差控制在±1%FS以内,为半导体芯片制造、生物制药等高端产业提供可靠的水质保障。